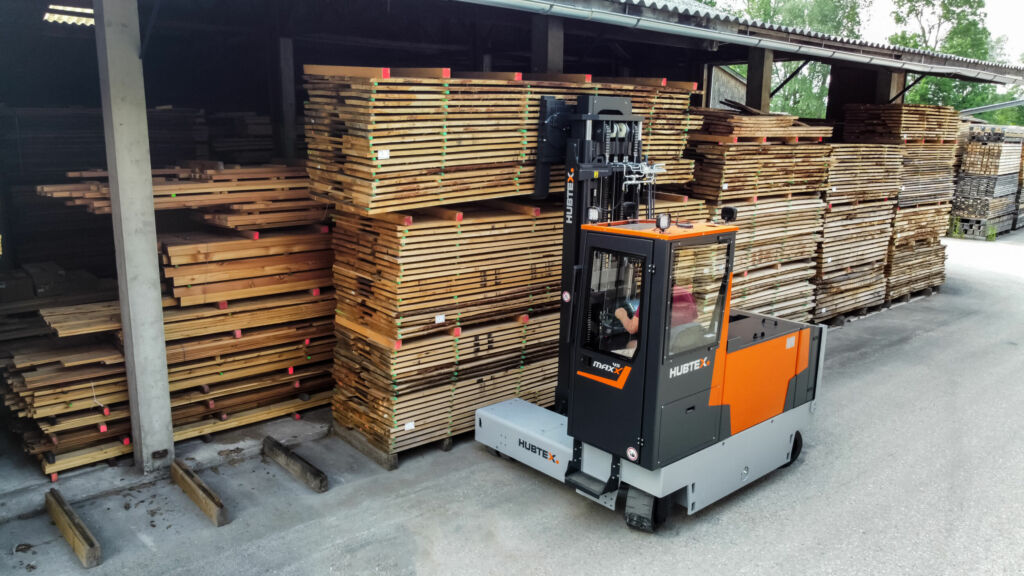
In puncto Stromverbrauch nehmen Flurförderzeuge (FFZ) und Fördertechnik mit durchschnittlich 20 bis 50 Prozent einen großen Anteil bei den Energiekosten in der Holzbranche ein, vor allem seit der steigenden Elektrifizierung der Flotten. Der Anteil an verbrennungsmotorischen Fahrzeugen im Produktportfolio vieler Hersteller sinkt seit einigen Jahren – ein Trend, der sich fortsetzen wird. „Die größten Einsparpotenziale liegen eindeutig bei Elektrofahrzeugen: Schließlich verbrauchen sie wenig Strom und emittieren deutlich weniger CO2“, erklärt Michael Röbig. Er ist Experte für das Energiemanagement bei Hubtex, einem der führenden Hersteller von spezialgefertigten Flurförderzeugen, Seitenstaplern und Kommissionierfahrzeugen für lange, schwere und sperrige Güter. „Für jede Einsatzanforderung empfiehlt sich ein Antriebskonzept, das zu den individuellen Gegebenheiten vor Ort passt. Bei der Beratung ist es deshalb wichtig, sich ein ganzheitliches Bild von den Arbeitsabläufen zu machen.“
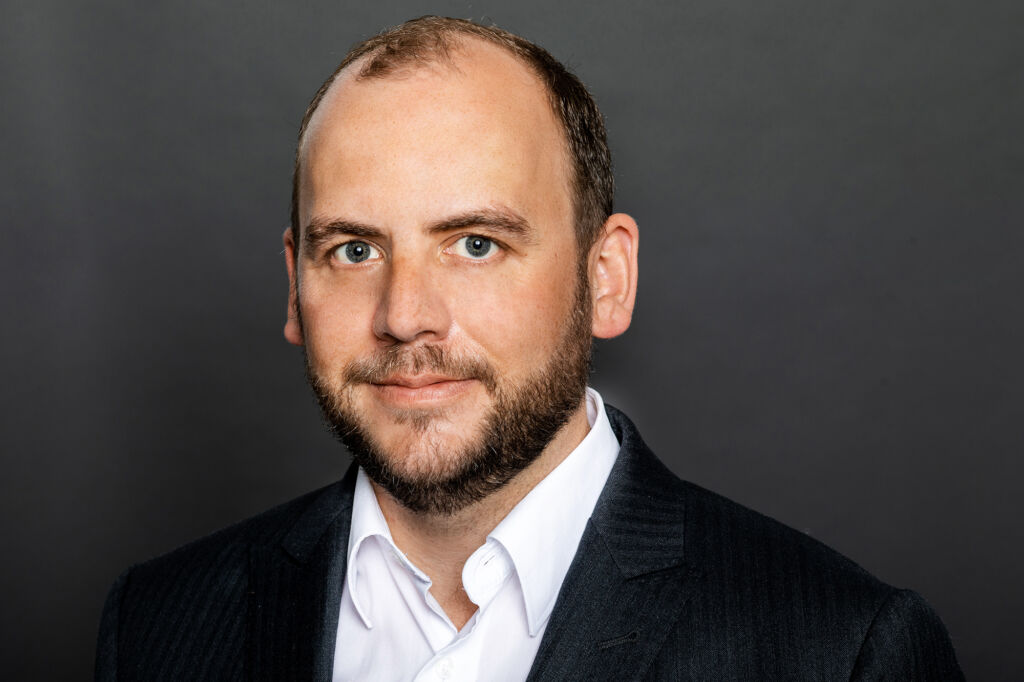
Energiemanagement in der Holzindustrie
Die geschickte Planung aller Faktoren erzielt hohe Zeit- und Kostenersparnisse. Zum anderen kann der Anwender mit einem entsprechenden Energiekonzept die Leistungskapazitäten seiner Maschinen wesentlich effektiver nutzen. Möchte ein Kunde ein neues Fahrzeug erwerben, werden seine Anforderungen so weit wie möglich erfasst: Wie sieht ein typischer Einsatz in diesem Betrieb aus? Welche Fahrleistung erbringen die Fahrzeuge? „All diese Parameter muss ein Berater bei uns ermitteln, zumal der Kunde diese Daten oftmals nicht selbst vorliegen hat“, erklärt Röbig. Ausschlaggebende Komponenten sind das Fahrzeug, die Mechanik und schließlich die Ausstattung, bei der das Energiemanagement ein wichtiger Schwerpunkt ist. Alles beginnt jedoch mit der Wahl des geeigneten Fahrzeugtyps.
Elektroantrieb vs. Verbrennungsmotor
„In den vergangenen Jahren fiel die Wahl aufgrund des wachsenden Umweltbewusstseins der Unternehmen aus der Holzbranche immer mehr auf elektrisch betriebene Fahrzeuge“, sagt Röbig. „Je nach Leistungskapazitäten und Einsatzszenarien, kann aber auch der Stapler mit Verbrennungsmotor die bessere Wahl sein.“ Um eine adäquate Kaufentscheidung zu treffen, sollten Anwender die Total Cost of Ownership (TCO) betrachten. In der Anschaffung sind Mehrwegestapler mit Verbrennungsmotor in der Regel günstiger. Die Kosten für Gas oder den Dieselkraftstoff sind jedoch deutlich höher als die für Elektrizität, ebenso wie für Verschleißteile und Reparaturen. Batteriebetriebene Mehrwegestapler benötigen im Normalfall lediglich einen sachkundigen Service, der die üblichen Verschleißteile wechselt, um die theoretische Lebensdauer von mehreren Jahren auch wirklich zu erreichen. Im Vergleich zu einem Verbrennungsmotor spart ein Elektroantrieb zudem etwa 45 bis 55 Prozent CO2 ein. Liegt der Fokus also auf einem aktivem Energiemanagement, sollte die Wahl auf einen Elektroantrieb mit einer Vielzahl von Auswahlmöglichkeiten fallen.
Vor- und Nachteile der Batterietypen
In puncto Batteriesystem steht der Anwender vor einer weiteren Entscheidung: Blei-Säure- oder Lithium-Ionen-Batterien? Beide Technologien haben Vor- und Nachteile. Unterschiedliche Typen garantieren je nach Einsatzgebiet andere Leistungskapazitäten: Klassische Blei-Säure-Batterien sind immer noch einer der am häufigsten eingesetzten Batterietypen. Sie haben je nach Ladegerättyp eine Ladezeit von fünfeinhalb bis vierzehn Stunden, wobei im Schnitt 1.200 Ladezyklen möglich und die Investitionskosten vergleichsweise niedrig sind. Bei Mehrschichteinsätzen mit hohen Betriebsstunden und mit schweren Lasten sowie bei Einsatzspitzen wie dem Saisongeschäft kommen diese Batterien an ihre Kapazitätsgrenze. Bei mittelschweren Einsätzen setzt man in diesen Fällen meist auf einen Batteriewechsel, der trotz der Notwendigkeit eines entsprechenden Equipments in der Regel schnell erfolgt. Abhilfe können in diesen Fällen Hochleistungsbatterien auf Blei-Säure-Basis mit höheren Leistungsreserven bieten. Neben höheren Strömen zeichnen sich diese Batterien auch durch höhere Lebensdauer mit bis zu 1500 Ladezyklen aus. Abgerundet wird die Auswahl durch Gelbatterien, die wartungsfrei sind, keinen Wassernachschub benötigen und sich ohne Beschädigungen sehr schnell nachladen lassen. Auf der anderen Seite steht die Lithium-Ionen-Batterie: uneingeschränkt zwischenladbar, niedriges Gewicht, rund 6.000 Zyklen und eine deutlich höhere Energiedichte als die Blei-Säure-Batterie. Durch den hohen Wirkungsgrad von circa 90 Prozent sind die Ladezeiten deutlich kürzer. „Es gibt mehrere Typen von Lithium-Ionen-Batterien, die sich in puncto Energiedichte, Leistungskapazitäten, Umweltverträglichkeit und Lebensdauer unterscheiden. In der Praxis wird uns häufig gezeigt, dass es wichtig ist, bei der Entscheidung auf eine Kombination aus Anwendung und sicherer Technologie zu setzen“, fasst Röbig zusammen.
Die Technologien in der Anwendung
Für welche Anwendung eignet sich demnach welche Technologie? „Die Lithium-Ionen-Batterie ist sinnvoll bei kontinuierlichem Betrieb. Bei einem Zwei- bis Drei-Schicht-Betrieb nutzt man die Pausen zur Zwischenladung. Wir bei Hubtex empfehlen Batterien ganz klar anhand der voraussichtlichen Lauf- bzw. Einsatzzeit des Staplers. Fahren Kunden z.B. weniger als 1.500 Stunden im Jahr, bleibt die Blei-Säure-Batterie das günstigere System“, skizziert der Energiemanagement-Experte. „Der Anwender sollte allerdings beachten, dass er bei Mehrschichteinsätzen Ersatzbatterien auf Lager halten und diese immer wieder austauschen muss. Der Vorteil ist hier, dass nur die Zeit für den Batteriewechsel zum Stillstand des Gerätes führt und keine Zeit für die Ladung berücksichtigt werden muss.“ Ein weiterer Aspekt ist das Gewicht: Eine schwere Blei-Säure-Batterie kann von Vorteil sein, wenn Fahrzeuge ein gewisses Gegengewicht zur Last benötigen. Bei einer Lithium-Ionen-Batterie gleichen dies zusätzliche Stahlplatten aus. Zudem kostet sie zurzeit das Vier- bis Fünffache einer vergleichbaren Blei-Säure-Batterie, verfügt aber auch über die fünffache Lebensdauer. Röbig rät: „Um eine Entscheidung zu treffen, gilt deshalb die folgende Herangehensweise: Der Anwender sollte die Lebensdauer der Batterie in Relation zu ihrem Preis und Einsatz setzen. Dies gilt insbesondere für die mittelfristige Entwicklung, da laut Herstellerangaben mit steigenden Preisen für Blei-Säure-Batterien und – im Gegensatz dazu – mit sinkenden Preisen für Lithium-Ionen-Batterien zu rechnen ist.“
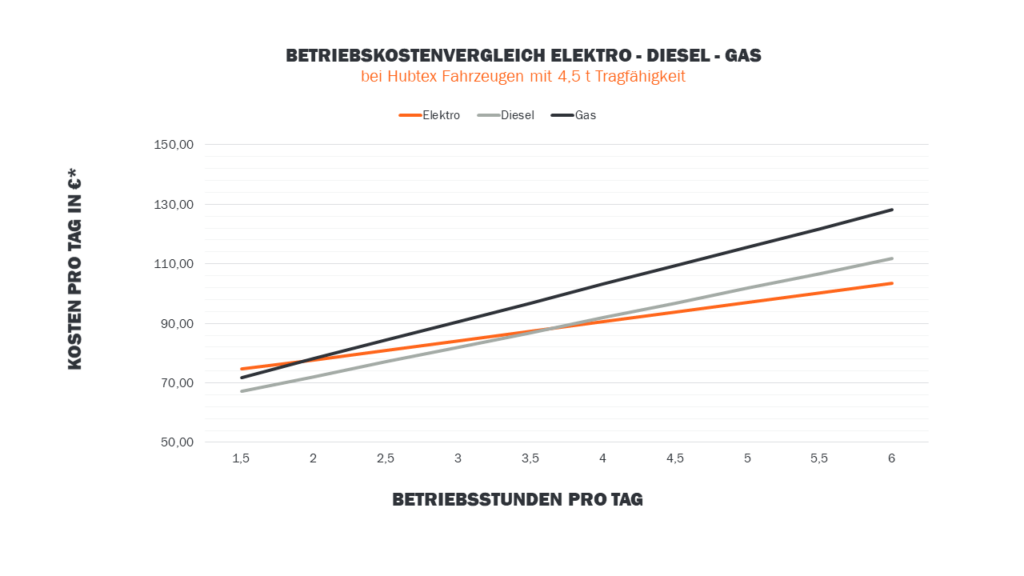
Nach der Batterie folgt das Ladekonzept
Ist die passende Batterie ausgewählt, stehen Maßnahmen zur Energieeinsparung beim Laden an. Dazu gibt es verschiedene Ladegeräte und -konzepte. Welche ist die perfekte Batterie-Ladegerät-Kombination für den jeweiligen Einsatz? Zunächst ist entscheidend, welche Technik verwendet wird. Die Systemeffektivität einer Blei-Säure-Batterie, die mit einem Hochfrequenz (HF)-Ladegerät geladen wird, ist wesentlich höher als beim Einsatz eines herkömmlichen 50 Hz-Ladegeräts. Die Kombination Lithium-Ion mit einem HF-Gerät ist in puncto Wirkungsgrad nochmals deutlich überlegen. Zudem überzeugen diese Ladegeräte trotz der höheren Anschaffungskosten durch ihre kompakte Größe, das geringe Gewicht und den niedrigeren Energieverbrauch. „Ob die eingesparte Energie den Mehrpreis in die bessere Ladetechnologie rechtfertigt, ist am Ende von den Betriebsstunden abhängig. Bei unseren Einschätzungen greifen wir daher auf fundierte Vergleichsberechnungen zurück, um Kunden die wirtschaftlichste Lösung aufzuzeigen“, erklärt Röbig. Nach der Auswahl der Ladetechnik folgt die Entscheidung für Batterieladeplätze und Wechselkonzepte. Auch hier ist für Hubtex der Batterietyp ausschlaggebend: Bei der Blei-Säure-Batterie ist neben der langen Ladezeit von acht oder neun Stunden bei Mehrschichteinsätzen vor allem der Zeitpunkt für den Batteriewechsel relevant. Mit einer Lithium-Ionen-Batterie kann man hingegen mit Zwischenladungen im Normalfall einen ganzen Tag abbilden. Passt das Konzept der Zwischenladungen, ist in der Regel kein Wechsel vonnöten. Es kann jedoch sein, dass die Lade- bzw. Energieinfrastruktur im Werk überfordert ist, wenn mehrere Fahrzeuge den gleichen Zeitraum für die Zwischenladung nutzen. Hier muss womöglich ein Energiespeicher dazwischengeschaltet werden.
Das richtige Handling im Einsatz
Das Handling der Batterie ist ein wichtiges Thema. Um die Blei-Säure-Batterie eines Staplers zu wechseln, ist ein zweiter Stapler oder ein Schwenkhallenkran vonnöten. Dieser Prozess kostet im laufenden Betrieb jedoch viel Zeit. Schneller sind Batteriewechselvorrichtungen, zum Beispiel Rollentische. Ein solcher Batteriewechsel ist unter zwei Bedingungen möglich: zum einen muss die Bauart des Fahrzeuges stimmen und zum anderen der Platz für die Vorrichtung vorhanden sein. Ein weiterer Aspekt, der in die Planung miteinfließen muss, sind Batteriewartungen: Das Risiko, Blei-Säure-Batterien falsch handzuhaben, ist hoch, da sie sich schnell in die Tiefentladung bringen können. So kann es zu chemischen Schäden an der Batterie kommen. „Im Gegensatz zur Blei-Säure-Batterie überzeugt die Lithium-Ionen-Batterie durch ihre Unempfindlichkeit. Weitere Arbeitsschritte, die bei dieser Technologie entfallen, sind der Arbeits- und Pflegeaufwand“, wie Röbig anmerkt. Beim Einsatz von Blei-Säure-Batterien müssen Befüllstationen eingerichtet werden, an denen der Anwender idealerweise bei jeder Ladung überprüft, ob die Batterie noch über genug Wasser verfügt.
Ausblick: automatisierte und andere Konzepte
Auch automatisierte Fahrzeuglösungen (AGV) erschließen zunehmend neue Einsatzgebiete. Zum einen, weil sie effektivere, sprich energieeffizientere Wege fahren und zum anderen alles selbstständig erledigen: Sie bewegen sich zur Ladestation, laden und fahren weiter. Das vereinfacht die Prozesse für den Lagerlogistiker – doch genau an dieser Stelle lohnt oft ein zweiter Blick. Ein AGV ist beispielsweise für einen 24-Stunden-Einsatz mit einer Lithium-Ionen-Batterie vorgesehen. Möchte man ein vollautomatisches Fahrzeug einsetzen, benötigt man kontaktlose Lademethoden über Ladekontakte oder induktive Ladetechniken. Sowohl die Batterie als auch die Ladetechnologie sind jedoch preisintensiv. Die Frage lautet an der Stelle: Ist der Preis in Relation zum Einsatz gerechtfertigt? Häufig werden zwar vollautomatische Fahrzeuge eingesetzt, das Verbinden mit der Ladetechnik wird dennoch durch einen Mitarbeiter übernommen. „Auch weitere Speichermethoden wie die Wasserstoff-Brennstoffzelle sind noch nicht so energieeffizient wie der elektrische Antrieb mit Lithium-Ionen-Batterien. Die Fahrzeugauswahl am Markt ist aktuell eher klein und die notwendige Infrastruktur entsprechend preisintensiv in der Vorbereitung. Trotz der geringeren Energiekosten eignet sich diese Technologie nur bei sehr großen Flottengrößen“, erklärt Röbig.