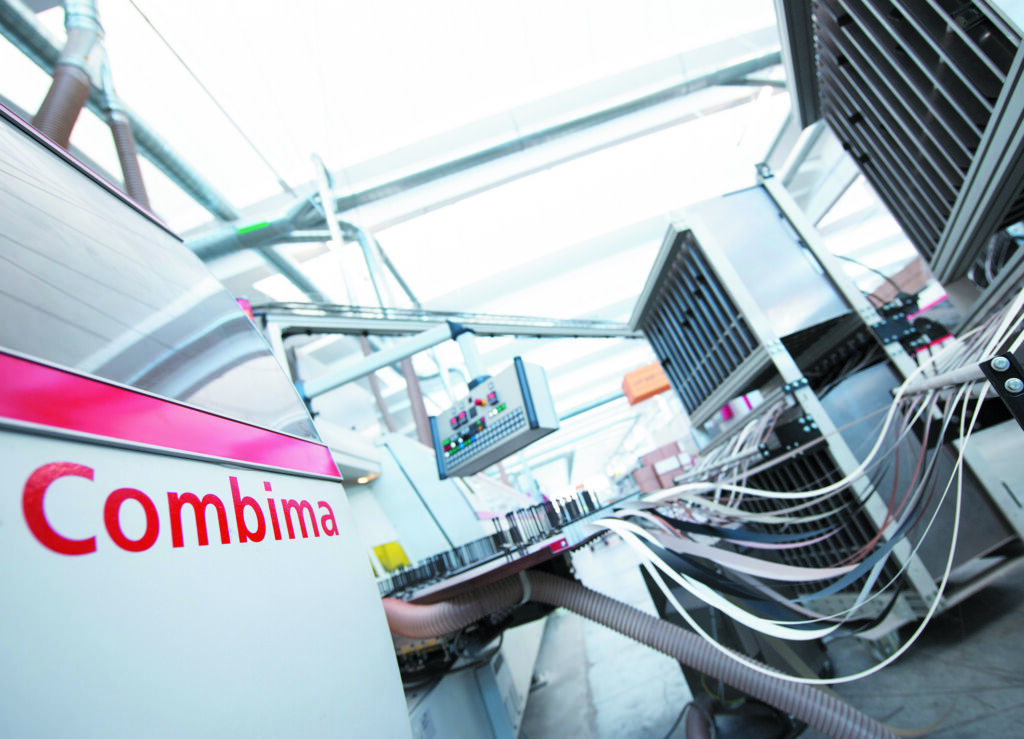
Mit Griffen oder ohne? Wer sich eine neue Küche anschafft, steht vor dieser Frage – und immer öfter entscheiden sich Käufer für grifflose Fronten. Eine klare Linienführung, eine moderne Optik, ein minimalistischer Look – das sind die ästhetischen Vorteile, die Kunden an grifflosen Küchen schätzen.
Wählen sie statt der Griffe allerdings Griffprofile, stellt dies einige Anforderungen an die Produktionstechnik. Bisher wurde dafür im Wesentlichen mit zwei Techniken gearbeitet: entweder mit Aluminiumprofilschienen, die an die Kanten montiert werden, oder mit Fronten aus MDF-Platten, in die das Profil gefräst und anschließend lackiert wurden. „Das sind beides jedoch sehr teure und aufwendige Arten der Kantengestaltung“ betont Dennis Reddig, Product Manager Edge Processing bei IMA Schelling.
Maschine für vier Profile und gerade Kanten
Der Maschinen- und Anlagenbauer hat nun für einen italienischen Kunden eine ganz besondere Lösung zum Fertigen von Griffprofilen entwickelt. Er wollte eine Kantenbearbeitungsmaschine, die sowohl gerade als auch speziell profilierte Kanten vollautomatisch produzieren kann. Vier verschiedene Profilarten sollten mit der Maschine gefertigt werden, neben J- und C-Profilen waren dies auch Schräg- und Falzprofile.
Vor allem die Bekantung der J- und C-Profile stellte die Experten von IMA Schelling vor eine Herausforderung. „Mit unterschiedlichen Kantenmaterialien und verschiedenen Arten des Klebstoffauftrags haben wir lange experimentiert, bis wir perfekte Ergebnisse hatten“, erzählt Reddig.
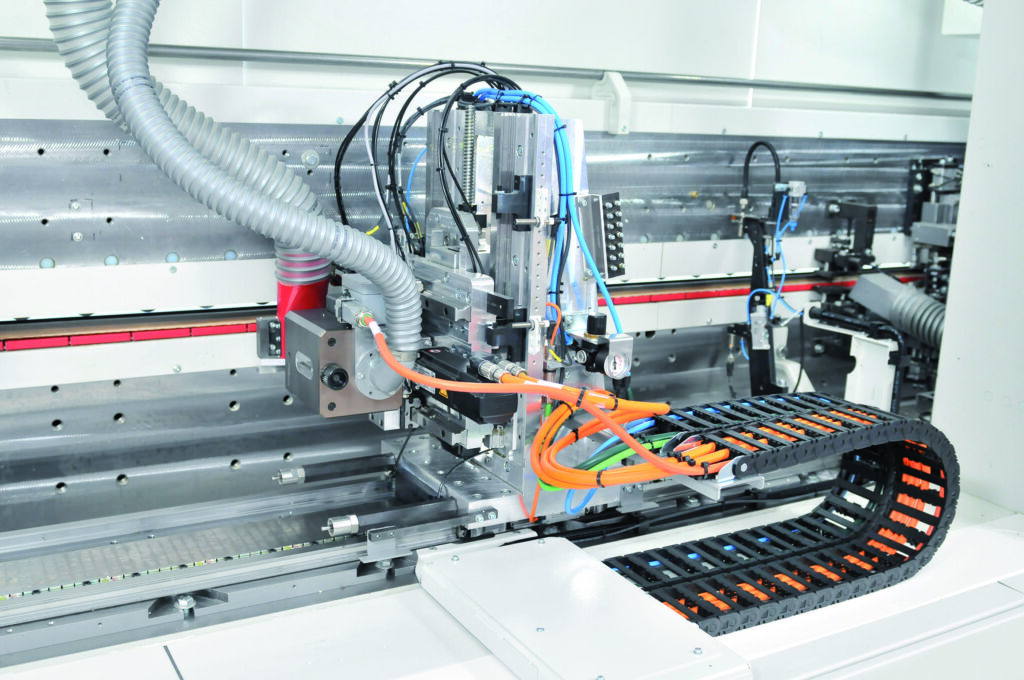
Herausforderung: Kantenmaterial
Softforming nennt sich die Bekantung fließender Formen, für die die Kantenhersteller auch spezielle Kantenmaterialien anbieten, die meist dünn und besonders flexibel sind. Doch in diesem Fall erwiesen sie sich als ungeeignet: Vor allem in den Mittellagen von Spanplatten zeichnete sich die Struktur der Späne im dünnen Kantenmaterial ab und war sicht- und fühlbar. Dieses Durchtelegrafieren sollte natürlich verhindert werden.
„Deswegen war klar, dass wir mit größeren Kantenstärken arbeiten mussten“, erklärt Reddig. Diese stellen nun aber große Herausforderungen ans Anbringen an die anspruchsvollen Profile. „Gerade bei dickeren Kanten sind die Rückstellkräfte groß und drücken die Kanten wieder aus der Rundung des Profils heraus“, so der Kantenexperte. Ein besonderes Augenmerk galt deshalb dem Klebstoffauftrag.
Herausforderung: Klebstoffauftrag
Bei den üblichen Kantenanleimmaschinen von IMA Schelling zur Bearbeitung gerader Kanten wird zuerst der Klebstoff aufs Werkstück aufgebracht, anschließend die Kante fixiert. Das lässt sich jedoch bei J- und C-Profilen kaum durchführen. „Wir haben zunächst das ausschließliche Auftragen des Klebstoffs aufs Kantenmaterial probiert und sind letztlich zu einer Mischung aus beiden Verfahren gekommen“, erläutert Dennis Reddig.
Nun wird der Klebstoff zum einen aufs Kantenmaterial, zum anderen – in speziellen Bereichen – direkt aufs Werkstück aufgebracht. Dazu hat IMA Schelling diverse Klebstoffauftragssysteme kombiniert und in die Anlage integriert.
Wie viel Klebstoff allerdings ausreichend ist, mussten die IMA Schelling-Experten erst ausprobieren. Zu wenig Klebstoff führt zu einer geringen Anhaftung, zu viel erfordert einen großen Nachbearbeitungsbedarf, um Klebstoffreste zu entfernen. Das kostet nicht nur Zeit, sondern birgt auch das Risiko, bei der Nachbearbeitung die Oberfläche zu beschädigen. Im Testzentrum in Lübbecke haben die Ingenieure von IMA Schelling eine Versuchsmaschine aufgebaut und sich sukzessive an die passende Kombination aus Form und Menge des Klebstoffauftrags herangearbeitet. „In vielen Versuchen haben wir schließlich den idealen Auftrag gefunden“, so Reddig.
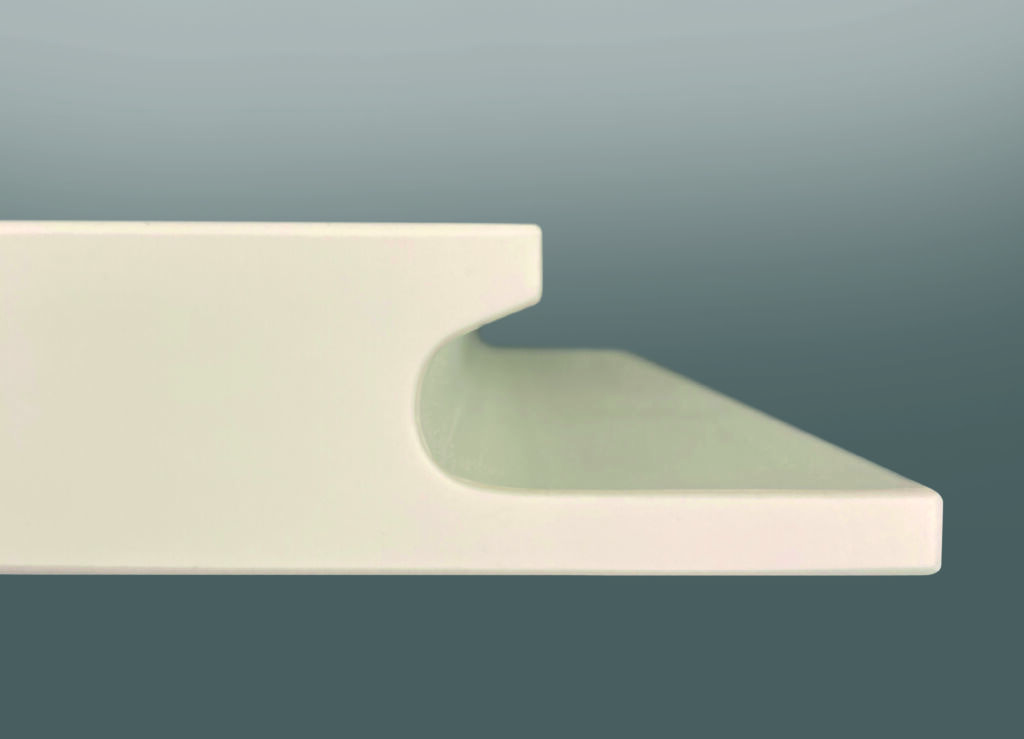
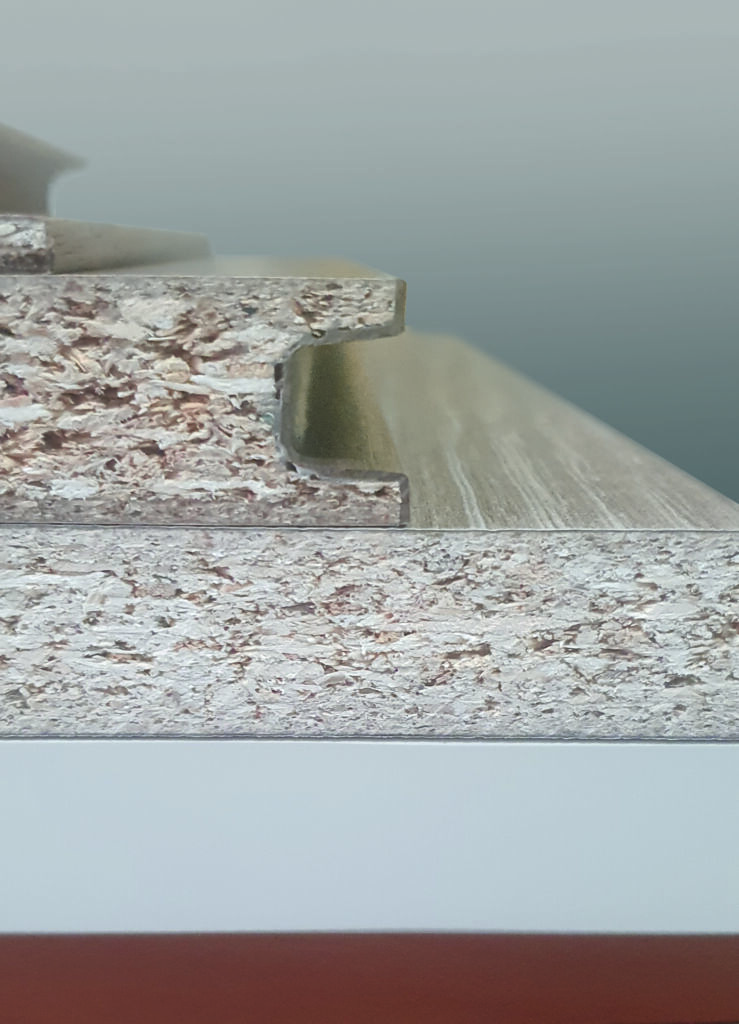
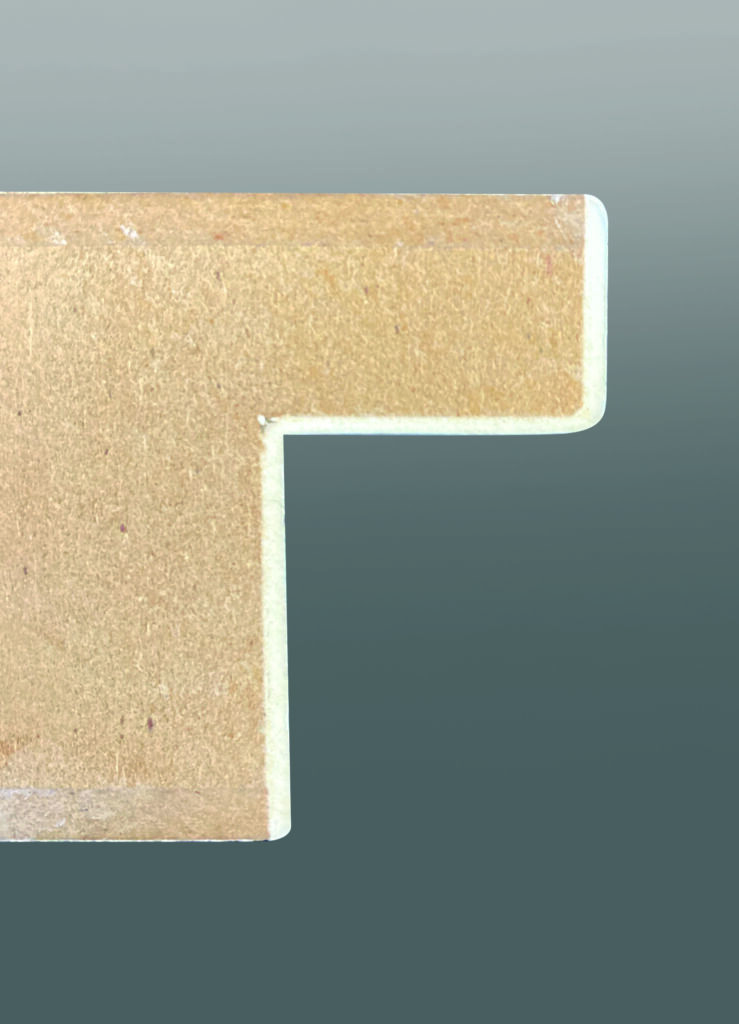
Herausforderung: Kantenstärke
Doch nicht nur an den Klebstoffauftrag stellt die Kantendicke besondere Anforderungen, auch an die Formbarkeit, schließlich setzt IMA Schelling hier Materialstärken zwischen 0,6 und 1,0 Millimeter ein. Gefragt war eine Lösung, mit der Material dieser Dicke um Winkel von fast 90° gelegt werden kann.
Auch dafür entwickelte IMA Schelling ein einfallsreiches Verfahren. Das Kantenmaterial wird einerseits an verschiedenen Stellen durch Heißluftgeräte elastisch gehalten. An besonders herausfordernden Positionen wird es außerdem mechanisch bearbeitet. „Wir setzen Ritzaggregate ein, um das Material an den entsprechenden Stellen gezielt zu schwächen, damit es sich um den Winkel legen lässt“, erklärt Dennis Reddig. Dabei stellte sich auch die Frage, wie stark der Eingriff ins Material sein durfte, damit dies nicht einreißt. Und auch dafür fanden die Ingenieure eine Lösung, die das richtige Maß hält.
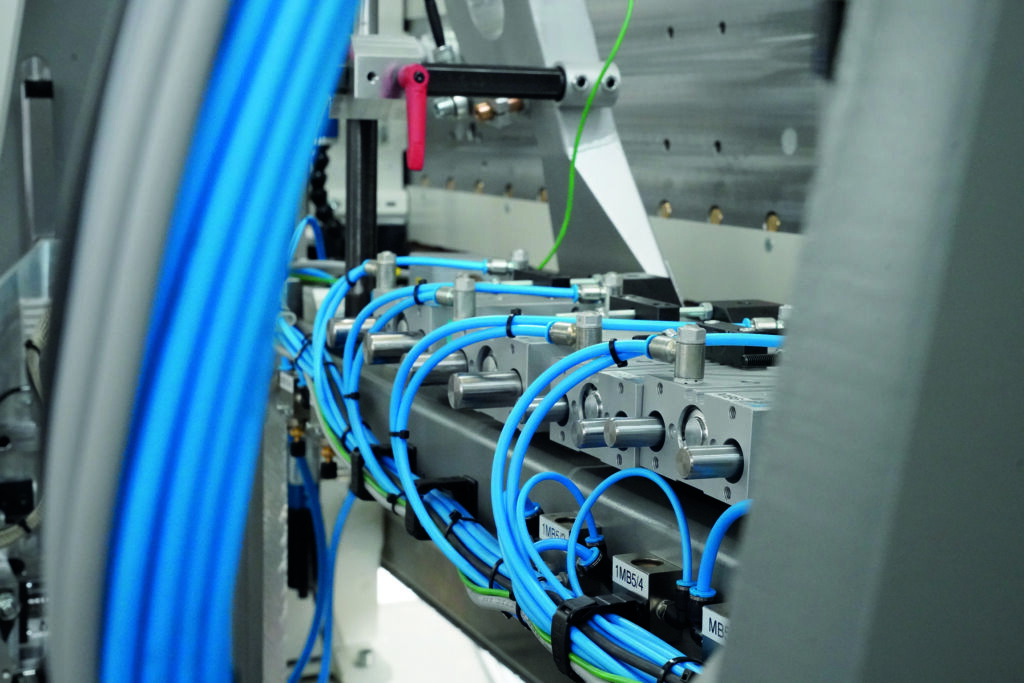
Fünf Kantenausprägungen im automatischen Wechsel
Die kundenindividuellen Lösungen integrierten die Engineering-Spezialisten in eine Format- und Kantenbearbeitungsmaschine Combima, die für die Losgröße-1-Fertigung ausgelegt ist. Der Kunde verfügt damit nun über eine All-in-Maschine für die vollautomatische Fertigung von Möbelfronten – sowohl mit geraden Kanten als auch mit vier unterschiedlichen anspruchsvollen Profilen. „Für die Anforderungen des italienischen Kunden haben wir eine leistungsfähige Maschine maßgeschneidert, die Möbelteile in fünf unterschiedlichen Kantenausprägungen im vollautomatischen Wechsel fertigt“, unterstreicht Reddig.
Damit die Maschine die zahlreichen Arbeitsschritte ausführen kann, hat sie verschiedene Werkzeuge im dauerhaften Zugriff und ist darüber hinaus mit mehreren Nachbearbeitungsaggregaten ausgestattet, wie dem Innenkontur-Fräsaggregat I-KFA, Profil- und Flachziehklingen, Schwabbelaggregaten und Bürsteneinheiten. Insgesamt kommt die Maschine für das Softforming mit Dickkante damit auf eine Länge von etwas über 40 Metern. „Für eine Maschine zur Bearbeitung von Möbelteilen ist das schon eine große Dimension“, erläutert Dennis Reddig. „Andererseits stellt sie auch eine ganz besondere Lösung dar, die in dieser Form einmalig ist.“
IMA Schelling – für jede Idee die perfekte Lösung
Die IMA Schelling Group entwickelt, konzipiert und produziert Maschinen und Anlagen für holz-, kunststoff- und metallverarbeitende Betriebe. Internationale Möbelhersteller zählen ebenso zu den Kunden, wie Flugzeughersteller oder anspruchsvolle Tischlerei-Familienbetriebe. Auf Basis seiner über 100-jährigen Erfahrung entwickelt das Unternehmen innovative Bearbeitungslösungen für modernste vernetzte Produktionen, zugeschnitten auf individuelle Kundenansprüche – bis hin zu vollautomatisierten Losgröße-1-Anlagen.
In vier Business Units entwickelt der Anlagenbauer intelligente High-End-Lösungen: Board, Woodworking, Precision und Consulting. Kunden können auf eine umfassende Expertise zählen – bei Zuschnitt-, Bohr-, Kantenbearbeitungs- oder Materiallogistiklösungen im Holzsektor oder bei Aufteil- und Handling-Lösungen im Bereich Metalle, Kunst- und Baustoffe. Individuelle Strategien für eine wertschöpfungsorientierte Unternehmensentwicklung sowie Consulting, Software- und Digitalisierungsprodukte runden das Portfolio ab.
IMA Schelling verfügt über ein globales Netzwerk von 17 Niederlassungen und 70 Vertriebspartnern und betreibt vier Produktionsstandorte in Deutschland, Österreich, Polen und der Slowakei. 2022 erwirtschaftete der Anlagenbauer mit weltweit 1.850 Mitarbeitern einen Gesamtumsatz von mehr als 309 Millionen Euro.