Auf die diesjährige Holz-Handwerk hatte Holz-Her eine breite Auswahl an Maschinen mitgebracht. Ob CNC-Bearbeitung, Kantenanleimen, Zuschnitt oder Nesting – der Maschinenbauer wartete mit einem Angebot für jeden Bedarf auf. Die meisten Besucher aber fanden sich an der Epicon 7245 ein: Das neue 5-Achs-Bearbeitungszentrum ist vielseitig einsetzbar.
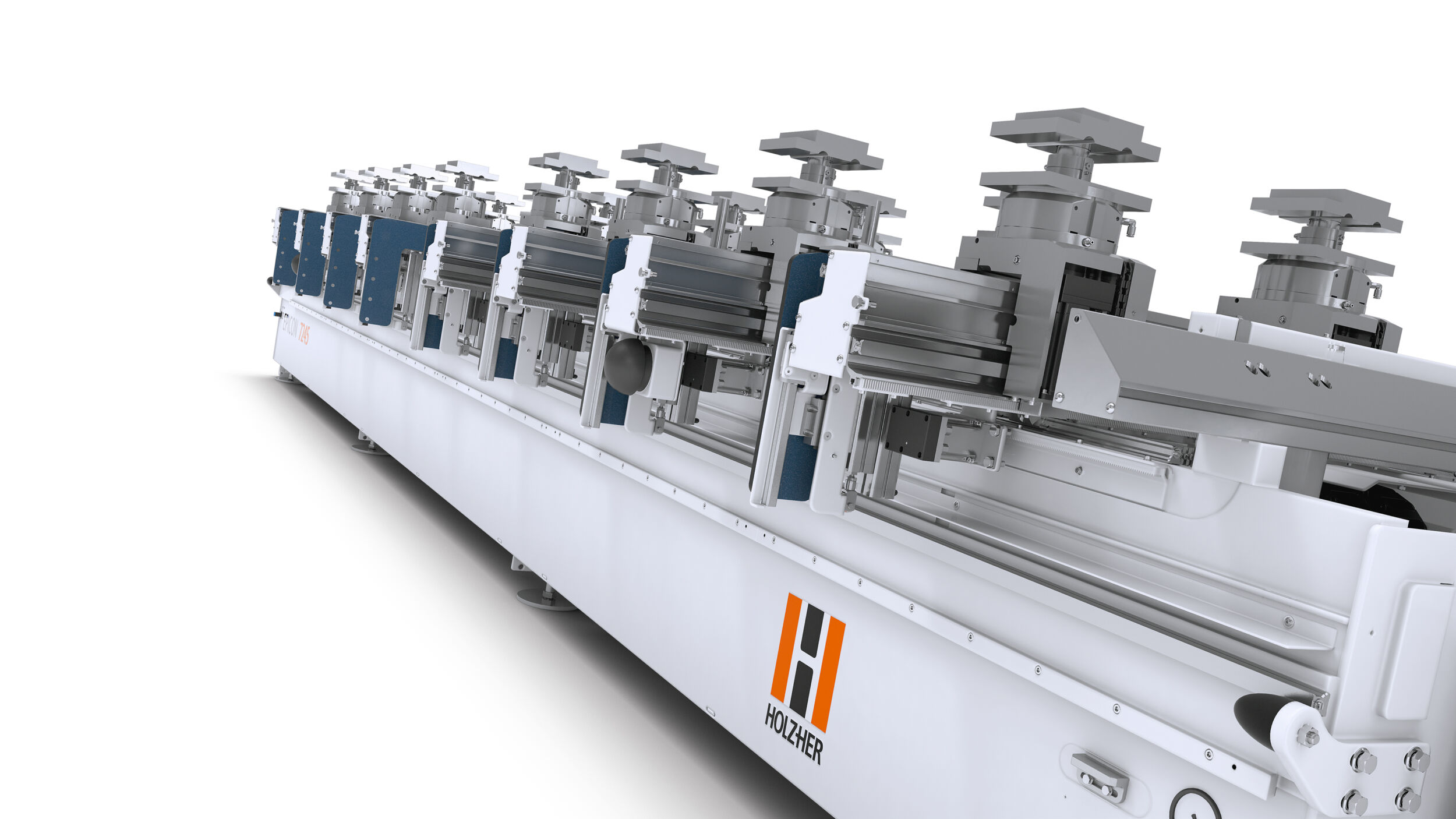